Design & Construction
Design & Construction
Wire Rope

Single Size The basic strand construction has wires of the same size wound around a center.
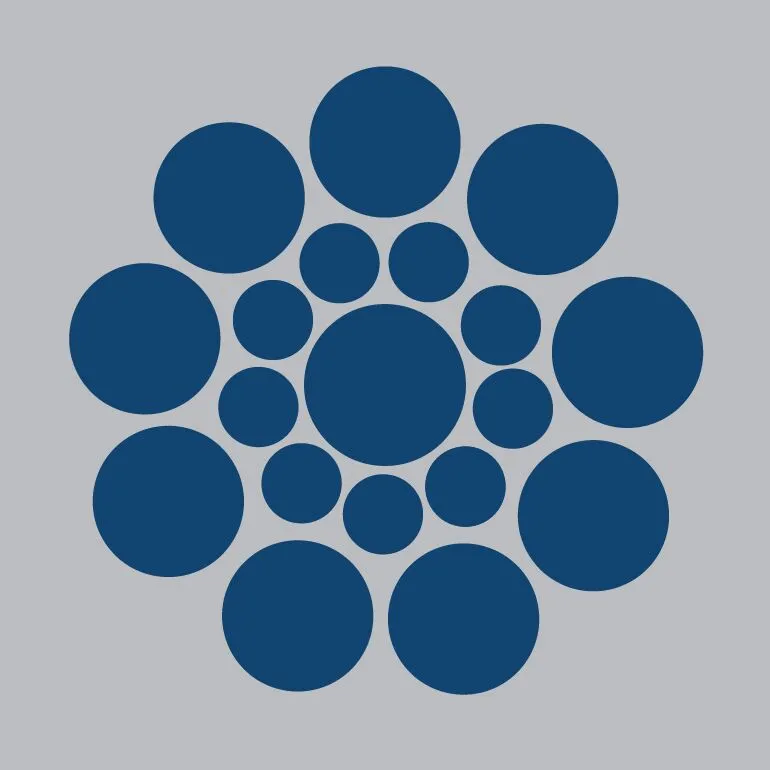
Seale Large outer wires with the same number of smaller inner wires around a core wire. Provides excellent abrasion resistance but less fatigue resistance. When used with an IWRC, it offers excellent crush resistance over drums.
Filler Wire Small wires fill spaces between large wires to produce crush resistance and a good balance of strength, flexibility and resistance to abrasion.
Warrington Outer layer of alternately large and small wires provides good flexibility and strength but low abrasion and crush resistance.
Seale Filler Wire Many commonly used wire ropes use combinations of these basic constructions.
Filler Wire Seale Many commonly used wire ropes use combinations of these basic constructions.
Warrington Seale Many commonly used wire ropes use combinations of these basic constructions.
Seale Warrington Seale Many commonly used wire ropes use combinations of these basic constructions.
Multiple Operation One of the above strand designs may be covered with one or more layers of uniformsized wires.
Wire ropes are composed of independent parts – wires, strands and cores – that continuously interact with each other during service.
Wire rope engineers design those parts in differing steel grades, finishes and a variety of constructions to attain the best balance of strength, abrasion resistance, crush resistance, bending fatigue resistance and corrosion resistance for each application.
To select the best wire rope for each application, one must know the required performance characteristics for the job and enough about wire rope design to select the optimum combination of wire rope properties.
The following information is presented as a basic guide. Bridon American engineers and field service specialists are available to provide more specific recommendations.
Strand Constructions
Strands are designed with various combinations of wires and wire sizes to produce the desired resistance to fatigue and abrasion. Generally, a small number of large wires will be more abrasion resistant and less fatigue resistant than a large number of small wires.
Finish
Bright finish is suitable for most applications. Galvanized finish is available for corrosive environments. Plastic jacketing and encapsulation is also available on some constructions.
Wire Grades
The most common steel wire grades are: IPS (Improved Plow Steel), EIP (Extra Improved Plow Steel) and EEIP (Extra Extra Improved Plow Steel). Stainless Steels and other special grades are provided for special applications.
Most wire ropes are made with round wires. Both triangular and shaped wires are also used for special constructions.
Generally, the higher the strength of the wire, the lower its ductility will be.
Core IWRC (Independent Wire Rope Core) provides good crush resistance and increased strength.
Regular Lay
Definition Most common lay in which the wires wind in one direction and the strands the opposite direction. (right lay shown)
Characteristics Less likely to kink and untwist; easier to handle; more crush resistant than lang lay.
Lang Lay
Definition Wires in strand and strands of rope wind the same direction. (right lay shown)
Characteristics Increased resistance to abrasion; greater flexibility and fatigue resistance than regular lay; will kink and untwist.
Right Lay
Definition Strands wound to the left around the core. (regular lay shown)
Characteristics Used in a few special situations – cable tool drilling line, for example.
Right Lay Left Lay
Definition Strands wound to the left around the core. (regular lay shown)
Characteristics Used in a few special situations – cable tool drilling line, for example.
Alternate Lay
Definition Alternate strands of right regular lay and right lang lay.
Characteristics Combines the best features of regular and lang lay for boom hoist or winch lines.